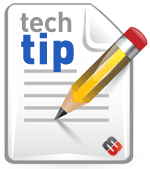
Adhesive bonding offers many benefits for joining similar and dissimilar substrates and has successfully replaced many traditional mechanical assembly techniques. These advantages range from even stress distribution, reducing risk of corrosion, gap filling/sealing capability, weight savings to automating manufacturing processes, enhancing quality, improving aesthetics, lowering production costs. They offer solutions to many challenging requirements and select formulations have demonstrated unmatched performance characteristics in demanding service conditions.
A basic understanding of the causes of adhesive or cohesive failure will mitigate the potential for any problems from occurring. When the adhesive separates (de-bonds) from the interface of the substrate or substrates this is an adhesive failure. In contrast when the adhesive material separates in the bulk layer of the bonding agent this is a cohesive failure. In many cases these failures may be hard to spot. Scrupulous consideration should be given by design engineers to follow best practices to ensure permanent bonds.
Most important in avoiding bonding failures is selecting the most appropriate adhesive compound. This system must be able to adhere well to the substrates being joined, withstand the environment it will be exposed to and maintain its properties over time. Conditions can range from temperature cycling, humidity, chemical exposures, different stresses, impact/vibration, shock and electrical insulation.
Also of prime importance is proper surface preparation for the substrates being mated. Different surfaces will require special preparation procedures. Optimum bonding surfaces should be clean, dry. They often need to remove oil, grease, loose surface deposits, contamination caused by cloths. Recommended surface procedures for select substrates may include abrasion, atmospheric plasma, flame treatment, corona. Plastic parts may contain residual mold release or wax on the surface which has to be removed with a suitable solvent.
Two part epoxy, silicone systems need to be mixed accurately by weight or volume. Inaccurate mix ratios can effect the properties and long term bonding ability. Proper curing is also essential in obtaining the proper effectiveness under the various service conditions it will be exposed to. It should be noted that the cure speed will be influenced by the temperature and humidity. Additionally the appropriate amount of pressure should be applied during the cure process.
It is important that the entire bond area be covered in the proper bond line thickness. If there is insufficient or nonuniform adhesive coverage this has the potential of causing cracking or separation between the mating surfaces. Voids and moisture absorption during the attachment process are of prime concern. Void can be caused by air entrapment which can be detrimental to the mechanical strength of the adhesive. Moisture absorption that accumulates during assembly can cause delamination. Another area of concern is residual stress during cure due to shrinkage or mismatched CTE of adherends. A combination of cleavage and peel stresses can cause bond separation.