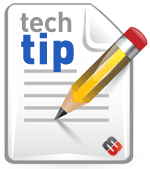
Depending on the shipping temperature, you may notice some changes in the viscosity of the epoxy by the time your shipment arrives. Read below to learn what to expect when you receive your epoxy shipment after shipping in very cold or very hot temperatures.
Two Part Epoxy Systems
With many two part epoxies, shipping at colder temperatures (below 60˚F) will usually cause Parts A and B to become noticeably thicker. If processed at colder temperatures, they are more difficult to mix, and cure more slowly. It is best to allow the system to return to room temperature in order to restore the normal viscosity, before mixing Parts A and B together.
When two part epoxies are shipped at higher temperatures, usually above 80˚F, you may notice that the system is thinner than expected. If processed at higher temperatures, the epoxy would be thinner and the working life would be shorter. Once the system returns to room temperature, its normal viscosity should be restored.
One Part Epoxy Systems
With many one part heat curing epoxies (which are not premixed & frozen), shipping in colder conditions will usually cause the viscosity to increase (just like 2 component epoxies). These epoxies can be gently heated to around 90-100˚F, and then be allowed to return to room temperature, to restore their normal viscosity.
When shipped at higher temperatures (such as 80-110˚F), these one part epoxies may appear thinner than expected. However, their working life would not be impacted, since they cure only at higher temperatures. Their normal viscosity should be restored when they return to room temperature.